Results/processes in terms of script, roles and ideas are reflected in our google doc: https://docs.google.com/document/d/14zxwJo6eB24SLhWYegINjtrimZ3LWMK9ZRYbWlZN47k/comment
It would be helpful to look at it when i refer to it.
The first thing we did when we met for the first time with our group is that we created a google doc where everyone has included what ideas they came up with for the “read” step. After further discussion, we decided to brainstorm two days later, when everyone has gone through all the other’s ideas.
Next time we met, we spent about an hour going back in forth about what we can do. We all really liked the idea of Douaa’s crime detection device + we came up with the glasses idea, (it perfectly aligns with the environment described by Ray Bradbury “The Veldt”, as it is a very advanced technology and could actually help parents detect that their children are attempting crime against them).
Then we started to think about the actual performance to further develop what our glasses are going to be doing and how we can show that.
We agreed that our performance should be entertaining, however kind of educational (in terms of how the glasses work) so that we don’t have to explain much, the show will be sufficient. Plus, we thought it would be relatable to set the scene in the classroom and involve some funny drama that would also make the performance more entertaining. Of course, we needed everyone to have a valuable role in that, so we almost evenly divided the roles (the google doc attached in the beginning of the blogpost has it on the first page).
And then, we remembered the dongles (Luciana said thats American for USB-C adapters). So yeah, we started writing the script and we were done in an hour. We suspected it was too short, but we decided to fix it during our first rehearsal that was happening the next day. We also needed some stuff to be done:
- signs “The following day”, “Next recitation” for transitions
- glasses
- (we would find out later that we also need a video frame, however at that time we were not planning on doing that as that scene did not exist)
As Zhuang Yi (I am not sure whats her english name) volunteered to be the narrator, so she also volunteered to create and to print out the signs. She had two days and had to bring them to out rehearsal. Spoiler: she has done a wonderful job! plus, apparently, she had to paint the letters herself! i was so amazed by the dedication she showed! (I’m just mentioning that in case she forgot to give herself credit for that in her own blogpost)
Anyway, the rest of the group, including me, gathered up the next day and started cutting out glasses out of the cardboard. At first, i thought that it would be better to cut out some huge glasses so that during the performance it would be extremely obvious that a teacher has put them on and (+ we settled for the idea of creating two glasses so that the second one could be painted red (spoiler: this would change later)) that they turned red when they do. I have created stuff like that: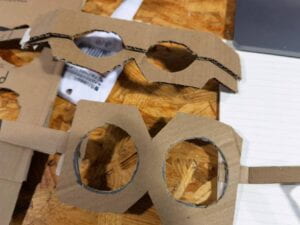
while I was trying to turn Ricky into a character from Marvel/DC instead of a teacher, Joy decided to shape glasses similarly to the glasses I had with me:
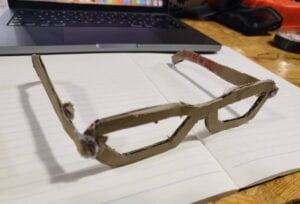
and, that was a great idea as they were the only ones that would actually fit Ricky (not fall down or make him look like Daredevil (Matt Murdock) the last reference to DC i promise). So, we decided to stick with it. The next challenge was that we had to come up with a way to actually show the interaction (the signal coming from the glasses). As I mentioned, the glasses were supposed to turn red. However, we didn’t have anything red that we could paint the glasses with. So we thought that we are going to go to FabLab the next day and hope they let us spray-paint the glasses red.
But everything changed as we thought that we would also like to do something with the non-red glasses as they looked kind of unfinished. And then the rolls of wire caught mine and Douaa’s attention. We had both red and soldering metallic wire there! So we took our chance and wrap the glasses with it. In the beginning, I was doing the soldering-wire, Douaa was doing the red one. However, We changed later as Douaa was struggling with keeping the wire wrapped around the glasses as she was using glue for that and it didn’t really work. I had an idea of using the soldering wire to do that (as it was much more “obedient” in that sense. And it happened! We spent around 15-20 min of that, and it was totally worth it! 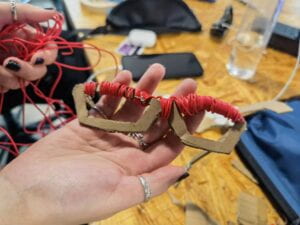
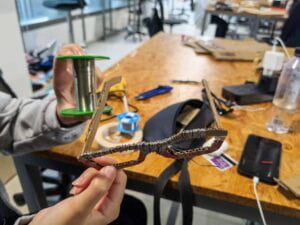
So yeah! the glasses were perfect and easy-to-comprehend artifact! And they were complete.
Moving on to the next day – the rehearsal – we spent some time working on the script as the initial one took place for 2 min only)))) so yeah, we extended the script, added some scenes (including the last one where the authority holds glasses and shows the projection of the video it recorded (the video of the crime). We added a couple of jokes, worked on our performance nuances such as the change of glasses and slow-mo scene and yellow duck to produce the beep sounds (initially the narrator, Zhuang, was supposed to do that)! I believe everyone has done a terrific job being as loud and clear in their speech and, I am proud of our performance and idea.
Side note: when we came up with the slow-mo scene (the last one) to show how the glasses work exactly, we decided to do this cardboard frame and Zhuang and Ricky went and started working on that, while me, Joy, Luciana and Douaa were finishing up the script! Later I helped Ricky and Zhuang to complete the frame (I glued some pieces together). I believe the frame turned out perfectly fine! 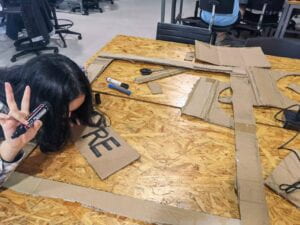
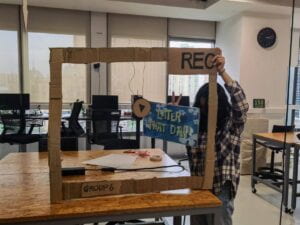
The day of performance we decided to rehearse our quotes once again and gathered up an hour before the class. We were kind of nervous, however dealt with it perfectly by reassuring each other that everything will be fine!
Performance went great! We were really happy that our invention also attracted some questions later and were very happy to answer them. Of course, there were some minor inconveniences, maybe we could’ve talked a bit louder and things like that, however, if i am being honest, this was the best one we have ever done! No one forgot their quotes or the times they enter the scene, everything was smooth and clear. I am not sure If we are supposed to attach the video here, but I will include it below in the blogpost.
Speaking of the questions, the following paragraph will describe the artifact that we have presented, including some details that came up during the Q&A:
Our invention was the Crime Detection glasses. This is an invention that perfectly fits into advanced-technologies environment of Ray Bradbury’s “The Veldt” as, besides being very fitting into the high-tech environment, it would also be a very helpful thing to have to detect the crime the children were plotting. Our glasses is basically merge of security cameras (recording), AI (algorithm that can actually record and show the needed footage, “understand” when the crime happens) and Google glasses (shape inspiration). The reason why we chose glasses (not just some sort of camera) is that it is, firstly, looks cooler, the second is that they would be more interactive (with the buttons that show the crime scene and instant reaction: turning red and beeps), and finally, more personalized experience (the person who wears them can control them). It also is more fitting into our understanding of interaction. So yeah, this object was unique, quite comprehensive in the way it works and fun to show to everyone else!
Again, I am very proud of our team for investing quite a lot of time and energy in brainstorming ideas, creating the artifact and other things for the performance and doing our best showing our invention! We were able to divide tasks efficiently, be creative, improvise and react rapidly to unforeseen circumstances (e.g. the absence the frame)!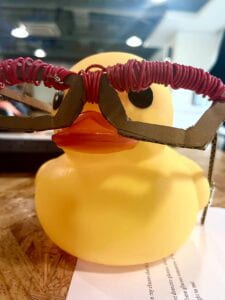
the video: